What is Labor Cost? 6 Strategies to Improve
It is difficult to navigate today's economy in the United States and remain competitive. A superior product or service isn't always enough to overcome poor market conditions or internal bottlenecks that are impacting profits.
Because labor costs constitute 30-35% of overall revenue, finding ways to minimize these expenses is essential for a company to meet key objectives.
Maximizing efficiency by investing in new techniques and software solutions can decrease labor expenses, optimize productivity, and improve the quality of output.
What is Labor Cost?
Labor cost is the total expense of employee wages and benefits to an organization. This may include payroll taxes, health care expenses, insurance benefits, paid time off, and production costs. Calculating labor expenses helps business leaders determine how to price their products and services to maintain profitability.
Labor cost is divided into indirect and direct expenses. Direct labor costs are all of the wages and benefits for workers that are directly responsible for manufacturing a company product or service.
Indirect labor costs or overhead costs' are any additional expenses that include wages paid to workers who indirectly support a product or service, but don't actually produce it.
Labor costs are further broken into fixed and variable expenses. A variable cost fluctuates depending on the output of produced goods and the health of the market. Fixed expenses do not fluctuate regardless of how many products or goods are produced.
For example, a variable cost includes sales commissions and any equipment used to manufacture a product. A fixed expense includes rental lease payments or property taxes.
Properly calculating the labor cost percentage helps to know how to price total sales items and optimize cash flow management. To decrease labor costs and maintain profitability, an organization must first compile every single expense related to labor. It should then pinpoint inefficiencies or cost savings opportunities, which is often difficult to do.
Businesses that want to maintain the same number staff and pay employees a fair wage can find many other hidden areas where wastage occurs. Best practices to cut costs include
1. Combine Vacation and Sick Leave
Absenteeism is expensive and it decreases employee morale, which further impacts labor costs. To minimize absenteeism and decrease labor costs, owners should combine paid vacation and a smaller amount of sick leave into one package.
For example, if a company offers one week of vacation per year and one week of sick leave per year, it may instead offer 10 days off a year for employees to use as they wish. This decreases the number of paid time off days while providing an incentivizing vacation benefit.
2. Invest in a Timekeeping System
Traditional timekeeping systems are inefficient and costly. It's easier to forge hours on a timesheet or be too generous in rounding minutes, particularly if supervisors aren't holding anyone accountable.
Business owners should instead invest in an optimized and automated timekeeping system to maintain accountability.
These systems send notifications when overtime is approaching or if an employee has failed to clock in on time. They also integrate with HR and accounting systems to ensure accurate payroll, which eliminates overpayments.
3. Stop Buddy-Punching
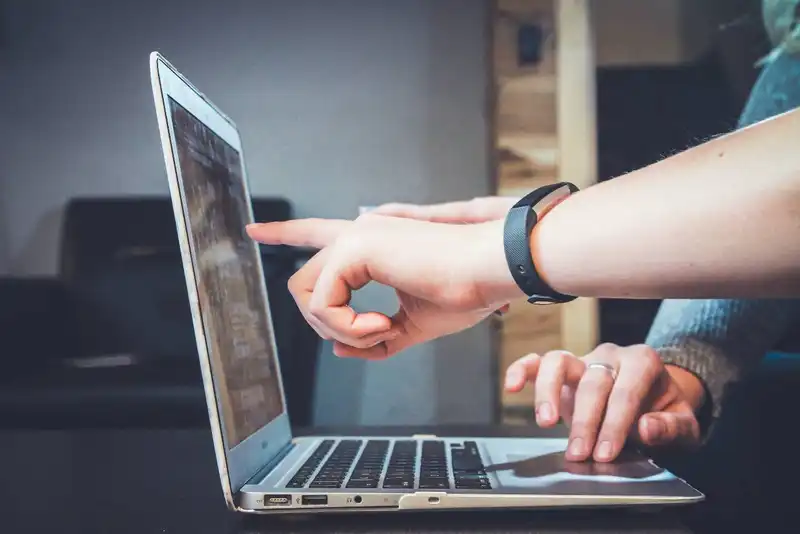
Buddy punching occurs when a coworker punches in for another coworker. It is a form of time theft that costs organizations thousands of dollars per year in labor costs. Business owners should invest in a biometric time clock to ensure that the person clocking in is who he/she claims to be.
This type of clock uses a portion of a fingerprint or face and matches it to a pre-stored image in a database to verify a person's identity. Its functionality integrates with mobile phones, which can be particularly helpful if employing remote workers. This will ensure timekeeping accuracy and prevent theft, which improves labor costs.
4. Monitor Overtime
For many states, overtime pay is hourly rate and a half, which can quickly add to total cost if used improperly. Business owners should work with the HR team to craft a specific overtime policy that limits usage and requires permission from authorized individuals.
Automated timekeeping and payroll software can also assist in accurately tracking employee hours by notifying management of approaching overtime, which can help to cut down labor expenses.
5. Improve Knowledge Management
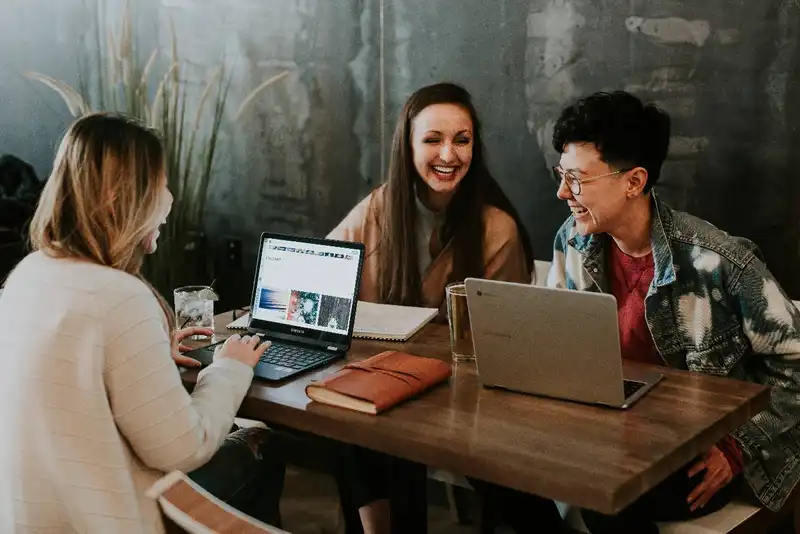
Employees typically need to ask questions throughout the day to perform their jobs. While this is essential for quality control and morale, it is time-consuming and repetitive to answer the same questions over and over again. This is particularly true for the HR department, as workers frequently ask questions about paychecks and healthcare plans.
An organization can streamline this process by investing in a self-service software system or intranet. Employees can easily view HR policies and other important information, which saves time. It also further improves productivity and ensures financial goals are met, which helps to improve labor costs.
6. Invest in Improvement Software
An organization should always look for ways to improve workflows to make them more efficient. Many different software solutions can automate this process, remap workflows, track the progress of tasks, and measure employee performance.
This will make sure resources are used efficiently, improve accuracy in data analysis, and increase accountability throughout the organization. Optimizing productivity and task management will save time and resources, which further minimizes labor costs.
Key Takeaways
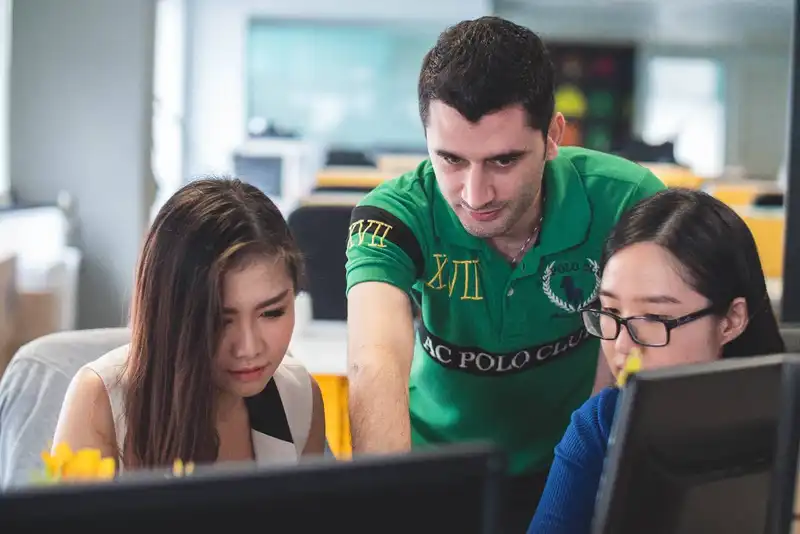
In conclusion, here are the key strategies to improve labor costs
- Organizations should combine vacation time and sick leave to improve employee morale, decrease paid time off, and minimize labor costs. A timekeeping system can also help accurately track employees work hours and eliminate overpayments in payroll.
- Eliminating buddy-punching by investing in a biometric time clock will decrease labor costs and decrease time theft. Implementing a specific set of policies to minimize overtime will also assist in decreasing overpayments.
- Owners should invest in the intranet or other software systems that allow employees to answer their questions. This will increase productivity and minimize waste, which can impact labor costs.
- Various improvement programs and task management software can monitor workflows, decrease inefficiency, and improve accountability. This increase in productivity will help to improve labor costs and minimize waste.