Clear Cut Examples of Direct Labor Costs
Running a successful business requires capital, resources, and effective budgeting. Decisions are made every day to boost profit margins and minimize waste.
For example, it's critical to optimize the onboarding process to employ effective teams without overspending. Purchasing less expensive materials to save money may seem like a good idea, but it can also impact the quality of outcome and customer satisfaction.
A critical area of operations is managing labor costs. Because labor expenses constitute such a large part of revenue, it's important to minimize them without hurting the quality of deliverables.
Successful companies regularly calculate their direct labor expenses to correctly price sales items and effectively manage their cash flow.
Direct Labor Cost Examples
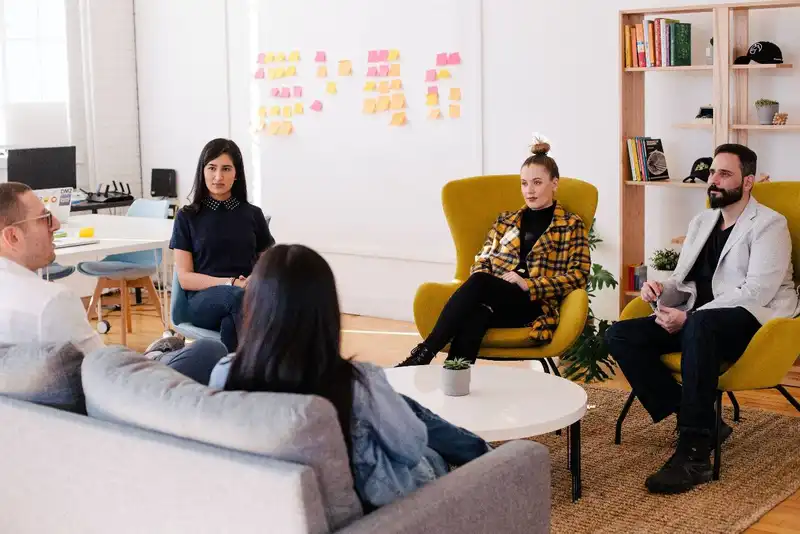
Labor costs include the totality of employee pay and any additional expenses such as payroll taxes or benefits. Labor costs are divided into direct expenses or indirect expenses. Direct labor costs are any expense directly involved in producing a product or service.
Indirect costs are also referred to as overhead expenses and are not directly related to producing a product or service. They include the wages paid to employees whose requirements allow others to manufacture products and services.
A company pays much more than simply the wage owed to a worker because there are numerous indirect expenses to factor in. Knowing exactly what direct and indirect expenses there are can help to perform accurate calculations.
Managing direct expenses properly assists in budgeting, cash flow management, and calculating the product cost or sales price. It can also pinpoint where waste is occurring so the company can minimize any overpayments or inefficiencies.
It optimizes decision-making by helping to know which customer projects or business activities to take on, as labor expenses chip away at profit margins.
It is critical to know exactly what is considered a direct cost. Though every company operates differently, here are the most common direct expenses to list when calculating the total cost of labor
- Wages- Salary or non-exempt hours worked for employees who directly produce a product or service
- Payroll Taxes- Any payroll taxes for workers who are directly responsible for producing a product or service
- Benefits- Paid time off or paid sick leave for these workers
- Insurance- Health or life insurance payments to these employees
- Worker's Compensation- A Form of insurance that protects companies when these workers are injured on the job
1. Furniture Manufacturer Cost of Labor Per Month
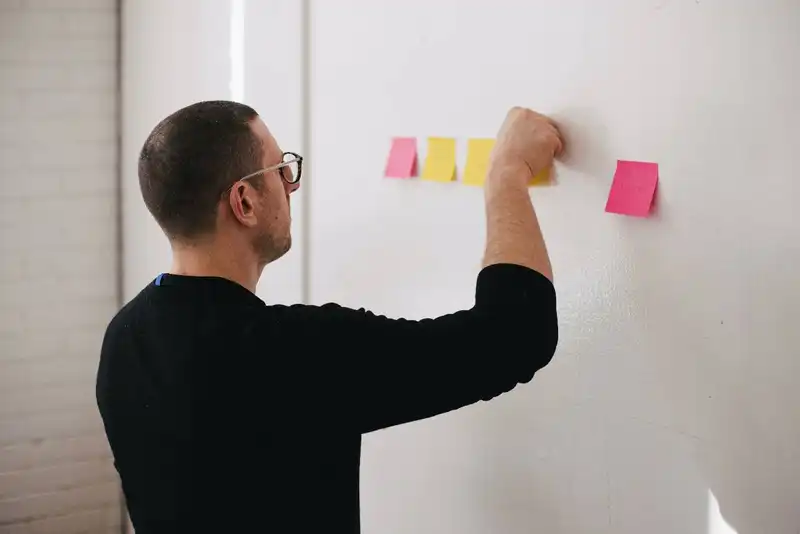
In this example, a business is calculating the total expenses for one month, which include -
- Wages- Employee pay for everyone responsible for manufacturing furniture. Total is $80,000
- Raw Materials- Wood and other materials purchased from suppliers used to produce furniture is $300,000
- Additional Wages- Wages for all workers who are not directly responsible for producing furniture is $90,000
- Insurance- Insurance premiums paid to workers directly related to producing furniture is $4,000
The raw materials are referred to as a direct material cost because they are needed to produce the furniture, but are not related to actual employees. The additional wages paid to workers who don't directly manufacture the furniture are referred to as indirect labor costs.
To calculate the total direct costs for one month, the furniture manufacturer should use this formula-
Total Direct Wages ($80,000) + Direct Insurance Payments ($4,000) = $84,000
2. Furniture Manufacturer Advantages and Disadvantages

Separating the direct labor expenses from the total labor expenses assists in understanding how the wages and benefits are not the same as the materials required to manufacture the furniture.
While both are direct costs, wages and benefits are employee-related, while materials are simply used by those employees. Direct materials are part of the production process (production costs), and are not labor costs.
Dividing these costs improves the accuracy of budgeting, sales pricing, and cash flow management. For example, if the furniture store included the raw materials within the labor expenses, it may price a piece of furniture much higher than it should be, which would impact customer loyalty and lead to a decrease in sales.
Separating indirect from direct costs helps to know exactly how much the company needs to have on hand to pay workers who produce items. For instance, if market conditions are poor, the company may lay off indirect workers first because they are not as essential as direct workers.
A point of confusion or disadvantage is that there are many required materials used by direct workers to produce a product or service. Many businesses are confused about whether a production cost should be included in a labor cost when it is time to budget or price an item.
Dividing each expense is an effective solution because it helps to gain a true picture of the categories of costs. The business will know exactly how much is spent on indirect costs, direct costs, and production costs, rather than having potential overlap and confusion.
Key Takeaways
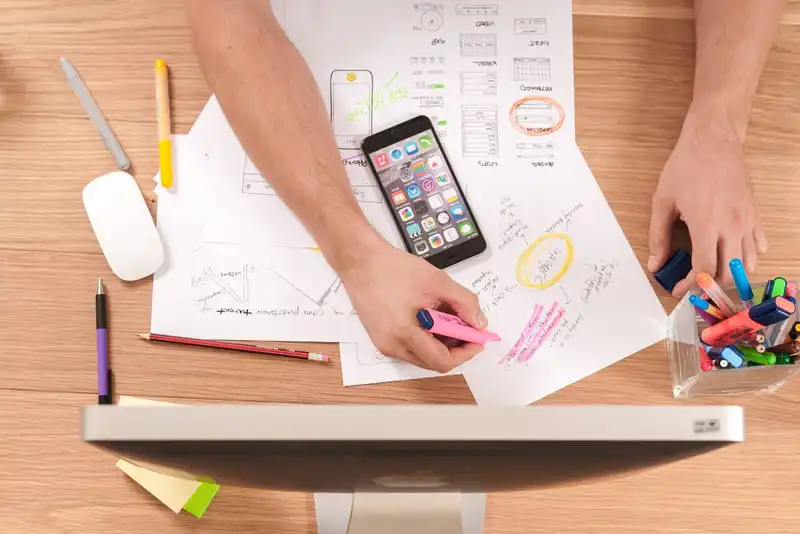
In conclusion, here is what to know about direct labor costs
- Direct labor costs are any expense directly related to the production of a product or service. Indirect, or overhead expenses are those unrelated to producing a product or service. Wages, payroll taxes, workers' compensation, and insurance are all direct expenses.
- To pinpoint the total direct cost of labor per month, a company should divide different expenses and then add the employee wages together with insurance payments to calculate the total.
- An advantage of performing calculations this way is that it improves the accuracy of budgeting, sales pricing, and cash flow management.
- A disadvantage or point of confusion is that it can be difficult to decipher which cost is part of the production and which is part of labor. Separating items in a highly organized manner will improve the accuracy of future budgeting.