The Future of Field Operations and Trends to Look Out For
The data-driven world has provided access to more information than ever before. Organizations can now develop deeper insights into inefficiencies and pinpoint solutions to optimize decision-making and reduce costs.
Because there is no end in sight to the digital transformation, manufacturers must learn to take advantage of these new technologies. In doing so, they can improve customer service, streamline operations, and minimize costs.
Field service companies from New York to California can particularly benefit from embedded sensors and other data collection mechanisms to ensure profitability and achieve business success.
How Field Operations is Expected to Change
Field operations is a type of service provided by manufacturers, internet service providers, construction companies, and other industries. It refers to installing, repairing, and maintaining a company-produced product on the customer's property rather than on-site.
Field operation managers oversee and execute the hiring of field technicians, assess their work quality, and create schedules to fulfill work orders. Field operators should also have an in-depth knowledge of the resources needed to comply with industry-related regulations.
Over the years, field work has become a profitable and growing enterprise in and of itself, rather than just a form of customer service provided by a manufacturer. With newer technologies that gather and analyze data collected from products, field operations will continue to evolve and grow. The most important trends to look out for include -
1. Greater Functionality of Workflow Tools
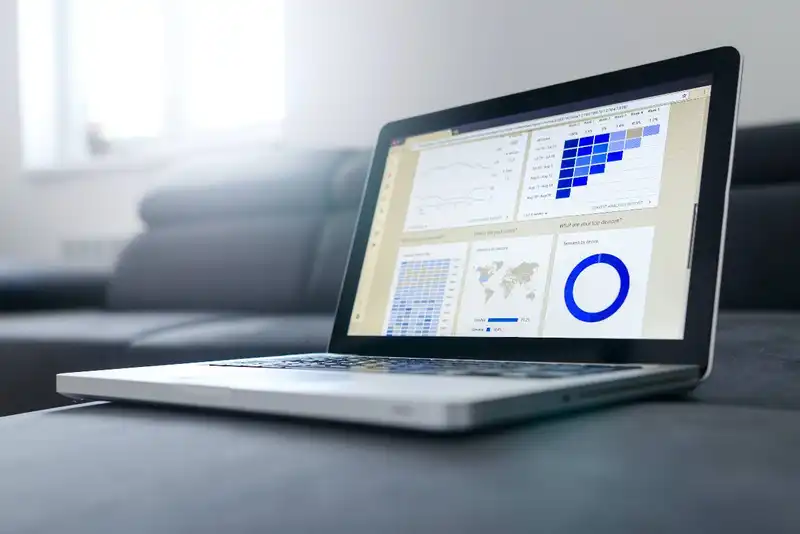
Traditionally, field service operators gathered collected data and put it into a business analytics tool, or dashboard. This helped managers gain insight into equipment failures, preventative maintenance requirements, and technician performance.
While this was a satisfactory way to assess fieldwork data, it didn't always provide the in-depth analysis required. Currently, more companies are investing in intelligent action boards to gain specific recommendations to address a problem, based on the data that is collected.
Because the insights derived from action boards provide specific recommendations, field operators don't have to use as much guesswork to resolve bottlenecks. For example, an action board may recommend visiting a facility to look through contract-related problems, insist on providing more training to a technician or tell a manager to follow up with an unhappy customer.
Rather than having to manually analyze dashboard-related data, operators are given a clear set of steps that assist in streamlining operations in accordance with industry-related regulations.
2. New Machine Learning Techniques
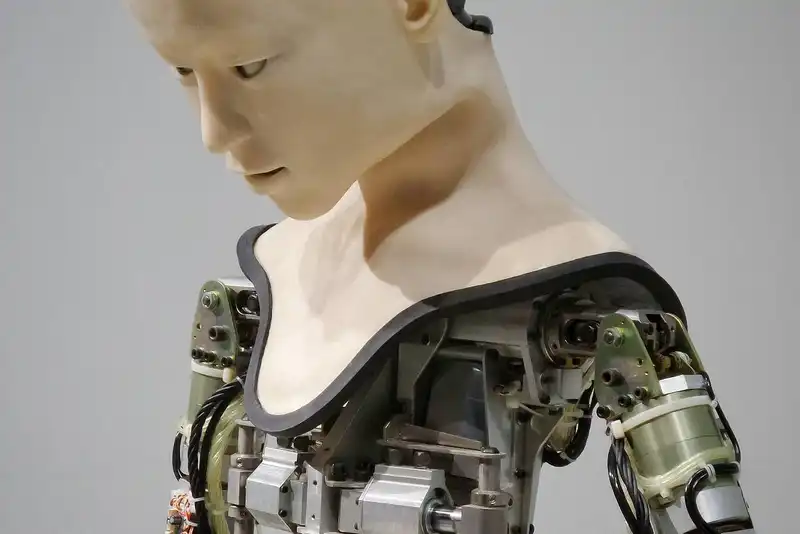
Developments in machine learning and artificial intelligence are helping operators predict maintenance requirements more effectively. Manufacturers can use embedded sensors and other applications to optimize asset management and improve real-time tracking.
Alerts are sent immediately to inform managers of an upcoming maintenance requirement, which helps operators provide better customer service. While breakdowns are less frequent due to these improvements in preventative maintenance, they do still occur. Thankfully, artificial intelligence can provide information to technicians that reduce the time needed to fix equipment.
Field workers also have access to expertise and on-demand assistance to shorten repair times and improve the quality of service. By utilizing AI and machine learning tools, field service companies around the globe have been able to reduce maintenance costs by approximately 15%.
3. AR-Enabled Tablets
Field technicians can utilize an AR-enabled tablet to shorten repair times and improve the quality of service. An AR tool assists in gaining insight into a non-functional piece of equipment through many mechanisms.
For example, technicians can place the tablet next to a piece of broken equipment to download a picture of what a healthy machine looks like. This easy access to knowledge optimizes customer service and minimizes time-consuming repair solutions, such as having to call another field worker to the worksite.
Though these technologies are not in widespread use yet, the oil/gas industry and other heavy equipment industries are currently employing them to improve work quality and customer satisfaction.
4. On-Demand Staffing Tools
Many companies are optimizing workforce management by investing in on-demand staffing tools. This works like an Uber-Esque business model, providing a marketplace where qualified technicians can input their information and schedules for field operators.
Field service companies use these tools to find the correct technician at the correct time, rather than relying on the same set of full-time employees. This can be helpful for companies that want to reduce labor costs or gain greater access to qualified workers for specific jobs.
Key Takeaways
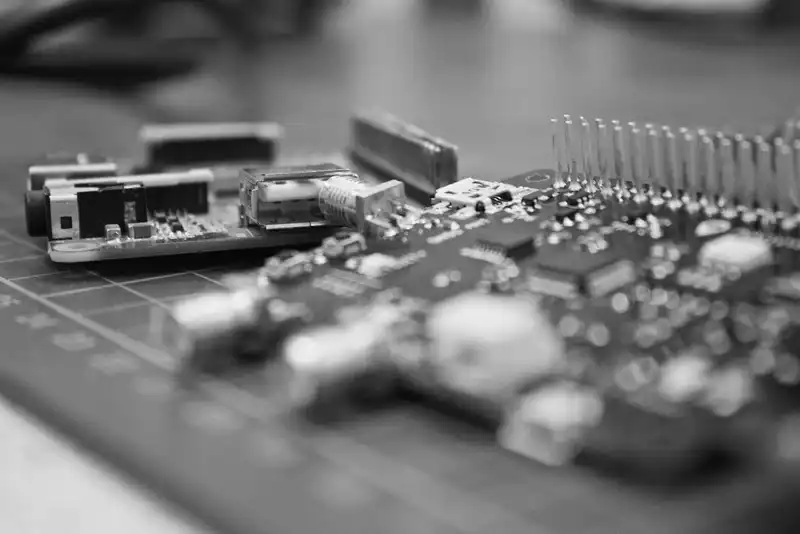
In conclusion, here are the top field operation trends to look out for
- Operators are investing in actionboards to improve the analysis of field data and make better business decisions. As a result of using an actionboard, companies have shortened response times, improved customer service, and optimized the quality of service.
- Machine learning and AI capabilities make it easier to track assets and improve preventative maintenance.
- AR-enabled tablets are now being used by a variety of industries to improve knowledge management and shorten repair times.
- Operators are using on-demand staffing tools to decrease labor costs, improve customer service, and streamline access to qualified workers.